This page will focus upon the installation of power venting on existing kilns or new kilns, with traditional vent placement in or near the roof. Kiln-direct hopes you will also consider power exhaust for hardwood kilns, this system was developed by Wooddryer System (R) and offers even better and more efficient venting.
First, lets take look at a standard kiln design which the industry has been building for decades. Now take a closer look at the direction of the venting and the direction of the general air flow.
Standard venting with
main fans in forward
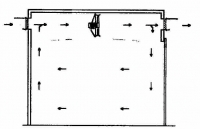
|
Standard venting with
main fans in reverse
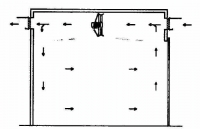
|
The direction of the venting and the air flow is the same. On the left drawing where the fans are running forward a vacuum is created on the left side and a pressure on the right side. The air will naturally enter the kiln on the vacuum side and exit the kiln on the pressure side. In most kilns, the heating coils are placed on both sides of the fans and represent the worst possible energy waste/loss scenario. Let us look at the venting process in 3 steps:
Step 1
First, we pull air in on the left side and mix it with the existing air in the kiln.
Step 2:
Then, the air goes through the heating and fan area causing the air to increase to a higher temperature or, in other words, we generate air with better drying qualities.
Step 3:
Now the mixed and heated air has reached the vent on the right side and some of the air is then vented to the outside. Lets consider this for a moment...we added air, heated it, and vented it; some of the air we pulled into the kiln was heated and thrown right back outside before it ever had a chance to dry any lumber, although it had all the potential to do so.
This design is mainly left over from the early design and for some reason, has remained the standard venting method for most of the kilns built to this day. In the early days when electric motors were expensive it made sense to avoid installing power venting, but since the 1970's there is no reason why power venting should not be utilized. Please allow us to try and explain the advantages of power venting and the benefits it could offer you on your existing kilns or on your next kiln project.
Power venting with
main fans in forward
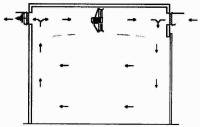
|
Power venting with
main fans in reverse
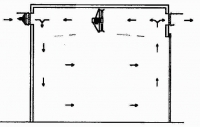
|
On the power venting it is very important to notice that the direction of the venting and the direction of the fans are opposite. The power venting is being used to overcome the natural venting pattern generated by the vacuum and pressure of the main fans. Let us look at the venting process in 3 steps and study how it is more energy efficient:
Step 1:
First, air is being exhausted outside right after it has existed the lumber. It is at this time, that the air has the lowest temperature but the highest relative humidity.
Step 2:
Then we add heat to the air, as it passes through the heat coils and the main fans in the middle of the kiln.
Step 3:
Now we are adding fresh air to the mixture before letting the heated air and the new air enter the lumber.
The power venting method is much more efficient than the standard venting system. In addition, it is also much easier to control, since we know how much air we will be venting, instead of relying on the main fans pressure and vacuum to accomplish this task.
To illustrate the difference, we have made this theoretical comparison between a standard vented design and the same design with power venting added to the same system. This will give you an idea on how to improve your existing kilns.
Standard venting
Power venting
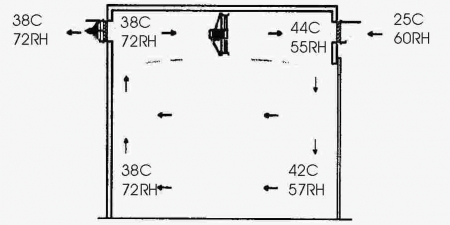
The above example is calculated/estimated. However, there is an obvious difference between the air temperature and relative humidity, which is being vented to the outside:
-- Standard vented: Existing air is 42C (108F) and 57% relative humidity.
-- Power vented: Existing air is 38C (100F) and 72% relative humidity.
It may not seem like a large difference, but 4C (8F) and 15% RH will amount to a lot of wasted energy when you consider that the kiln is operating nearly all the time.
General overview of advantages with power venting vs. standard venting.
More venting
In nearly all cases of installed power venting on your existing kiln, you will see a more powerful venting, giving you better control on fast drying species. This will especially hold true in the beginning of the drying process, when you are trying to remove the surface moisture.
Faster drying potential
Since you will probably have more powerful venting and less heat loss, you will have the opportunity to dry lumber faster (provided you have adequate air flow).
You must look carefully at your drying schedule and make sure that the lumber will allow itself to be dried faster, without increasing degrade and other drying defects.
More heat available
If your current heating system has difficulty in keeping the temperature, a power venting system will probably allow you to operate the kiln at a little lower temperature-without extending the drying time. By lowering the temperature and installing power venting, you have a two fold benefit:
-- First, the power venting system has wasted less energy than your previous standard venting system.
-- Second, the lower temperature in the kiln will provide a greater difference, between the steam coil temperature and the kiln temperature, thereby transferring more heat into the air.
Kiln-direct does not recommend installation of the old version in kiln venting. We strongly suggest that you consider power venting on your next kiln project and perhaps even consider installing it on your existing kilns.
If you would like to reduce the energy consumption further, we can suggest the installation of a heat recovery unit on the venting. Kiln-direct is currently in the final testing period of specially designed air to air, heat exchangers for kilns. These units use the existing hot and humid air to heat the incoming air, without mixing the two air streams together. Preliminary testing has shown a 20% to 40% savings on the heat requirements in the kilns. Please contact us for more information on the heat recovery units.