This power exhaust is a little bit different than the power venting. The power exhaust has an exhaust fan placed near the ground making it even more efficient. This design is especially suited for Hardwood kilns and high quality Pine kilns. The major drawback to this design is that we are always trying to vent, when the fans are running forward.
The kiln design described below is based on a design developed by Woodryer System,(R) and we are both, sharing and promoting this equally. The design has proven itself in high quality drying of white hardwoods. In addition, we have seen that this design is even more energy efficient now that the standard power venting is in or near the roof area.
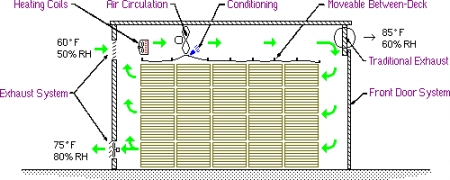
Air Circulation:
Kiln-direct's main fans can be used like any other kiln fans; however kiln-direct has a few improvements compared to the average kiln fans available:
-- All stainless steel venturi and motor mount.
-- Large kiln fans have all aluminum fan blades which are shaped for maximum performance in high static pressures and hostile environments- like a lumber kiln.
-- You can choose to buy the fan venturi and fan blade only and add the motor of your preference, or choose one of the motors we offer.
The fan can be placed in the middle as you would find them in a standard kiln, but we hope you will consider a little twist to an old idea. Kiln-direct suggests moving the main fans further towards the back side on hardwood kilns where we utilize the power exhaust system. This is really an intregrated design between:
-- Moving the fans towards the back
-- Installing the power exhaust, and
-- Using a control system, which allows for interval operated fans.
The placement of the main fans to the back will create a vacuum behind the lumber, which pulls air through the packs instead of blowing it. By creating a vacuum you will get a much more even air flow, resulting in both better and faster drying. Main fans are reversed to limit moisture spread throughout the kilns charge.
Exhaust System:
The biggest advantage of our exhaust system is the energy saving. By locating the exhaust system in the lower part of the back wall, the air with the highest humidity and lowest temperature (or in other words, the air with the least drying force) is expelled. Just compare the temperature of the exhaust versus the traditional design on the drawing above.
Heating Coils:
We prefer smaller heat units with a fan positioned behind the unit. They are easier to install, occupy less space, and improve air circulation. They can be used with either hot water or steam. A hot water system requires a lower investment, less operating, no chemical treatment, and lower future maintenance costs.
Conditioning:
We can use either steam or water spray humidifying depending on your current situation. A hot water heating system is generally at a lower cost to operate, but it does not provide the steam for faster conditioning. For non-steam systems, we use a water spray with a very fine mist allowing the mist to evaporate instantly. All this is controlled through our kiln controllers. However during the drying process our kiln controllers can either use the humidifying to keep the correct climate, or you can utilize the main fan interval system. This is another Wooddryer System innovation, which has proven its value all over the world. Please look under main fans for more information regarding interval operation of main fans. Adding water or steam to a drying process is, in our opinion, a waste of energy.
Moveable Between-Deck:
It is important to baffle the kiln correctly in order to insure that all the air travels through the lumber and not around it. Conventional baffling consists of a hinged plate at both ends of the stacking area. This method is well proven and works in many kilns. Kiln-direct suggests that you consider another and better baffling system. We call it a moveable between deck, because the whole between-deck moves up for loading. Once the loading has been completed the between-deck is lowered onto the top of the lumber packs. This system has several advantages over the traditional baffling system:
-- First we eliminate all the space over the stack. The flexible between-deck allows it to accept uneven loads as well. This provides better air flow through the lumber by eliminating the open space on top of the load.
-- Second we are crating more space over the between deck than the traditional version. The more open area provides lower air velocity and less resistance, thereby making the fans more efficient, since they have to overcome less total pressure.
-- Last, the flexible between-deck not only takes a little more punishment by forklift operators (within reason), but it is also easier to repair.
Kiln-direct suggests using a heavy duty tarp for the flexible membrane, which has 4 to 5 cross runners that are tied to a winch system. The most economical is a manual winch system, which can be operated by a large drill and a shepherd hook.
Main Door System:
Our main door systems are designed based upon the "lift and slide" principle. Kiln-direct can supply the door carrier system, all the latching hardware, and the gasket system. The door can be made on-site using local materials. Using the following:
-- Our components,
-- Our construction methods,
-- Your on-site labor, and
-- Local materials.
This combination will provide you with a very well functioning kiln door at a fraction of the cost, when compared to the panel type kiln doors. However, just as important, our kiln door construction has nearly eliminated thermal conductors found on most aluminum structure/panel solutions. A kiln door with no thermal conductors will not only save energy but it also prevents the water from condensing on the inside of the kiln door, which will help keep the correct drying climate inside the kiln. We believe our kiln doors are the most energy efficient in the industry.
Traditional Exhaust:
Our exhaust system has several advantages over the traditional exhaust design found on a majority of kiln designs. A traditional vent system is located on the top of a kiln, in the front, and back. On the drawing above, we demonstrate the difference between exhausting the air before (traditional exhaust) and after it has passed through the lumber.
The exhausted air is cooler and has a higher RH% with our system (which means less energy wasted) and it gives you the ability to dry lumber at lower temperatures even in the warmer climates.
We would like to know your opinion regarding this article. We encourage you to take a minute and send us an email to this adress
youropinion@kiln-direct.com It will help us to provide even better information to the next visitor.