There are many variations of the two general designs shown and described below; but in general they all resemble one or the other in their basic design. The baffles are generally a plate of some kind (material usage may differ). These baffles are normally hinged at the edge of the fixed between-deck and in one design we have seen a pneumatic inflated baffle, which is rarely installed. Actually, the second fixed between-deck design is really a dual long baffle system hinged at the bottom of the main fan header
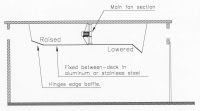
Between-deck with edge baffles
|
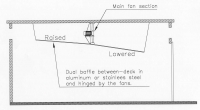
Hinged baffle between-deck |
Material used for a fixed between-deck.
Kiln-direct suggests you use a non-ferious metal, such as aluminum or stainless steel. When using stainless steel you will not need thick plates, since stainless steel is much stronger than aluminum. In addition, stainless steel is easier to weld even though harder to cut/shear and bend, but it will provide you with the best result for long time durability.
On older kilns and on very economy budgets steel is used. Any steel usage in a lumber kiln has some major drawbacks and will require more maintenance than aluminum or stainless steel. Another serious drawback is the potential condensation on the steel which can drip onto the lumber and discolor the surface. This is especially the case on oak, where the wood will turn nearly black from the reaction between the steel rust and the tanic-acid. Because of these reasons steel in any lumber kiln should be coated every 2 years to avoid corrosion. On older kilns you can often see a steel between-deck become a safety hazard, either from falling items or from a person falling through when he or she is walking on top during maintenance visits.
Kiln-direct strongly recommends that you do not use plywood or other wood products on large kiln installations, where a maintenance crew may be using the between-deck for maintenance. Wood products will deterioate in a lumber kiln, especially if the kiln has live steam spray for conditioning.
Operation of the baffles.
The edge type swing baffles are normally operated using a thin (3mm or 1/8") steel wire by simply pulling the wire down to a hook, which keeps the baffles up during loading and unloading of the lumber kiln. When the kiln is loaded the steel wire is taken off the hooks and the baffle is lowered onto the top of the lumber packs and prevents the air from cheating over the lumber packs. In some instances we have seen these operated using a small winch with several baffles on each. It should be mentioned that the edge type baffles normally consist of several individually operated plates. Each baffle plate is approximately 1.5-2.4 meters (5-8 feet) long.
On the fixed dual baffle-deck the operation of the baffle-deck is significantly heavier than the edge type baffle. For this reason a winch is normally used to lower and raise the baffles. A common method is to turn a pipe (50mm/2inch) on the back side of the kiln using a motor or manual winch. Upon this pipe you attach the wires from each baffle. As the pipe is turned the wire is wraped onto or off the pipe thereby raising and lowering the edge of the baffles, where these steel wires are attached.
Special design notice on a fixed dual baffle-deck.
It is important on both baffle systems that the baffles are sufficiently heavy to insure that the baffle stays on the lumber. On the dual baffle-deck system it is easier to design them too light, which will result in them being pulled up by the lifting force (push from below and vacuum on top) of the main fans. This is especially common, if it is made using aluminum profiles and plates.